Пористість, розриви порожнистого типу, утворені захопленням газу під час затвердіння, є поширеним, але громіздким дефектом при зварюванні MIG, який має кілька причин. Він може з’явитися в напівавтоматичних або роботизованих програмах і вимагає видалення та переробки в обох випадках, що призводить до простою та збільшення витрат.
Основною причиною пористості під час зварювання сталі є азот (N2), який потрапляє у зварювальну ванну. Коли рідина охолоджується, розчинність N2 значно знижується, і N2 виходить із розплавленої сталі, утворюючи бульбашки (пори). Під час оцинкованого/гальванічного зварювання випарений цинк може бути перемішаний у зварювальну ванну, і якщо немає достатньо часу для виходу до того, як ванна затвердіє, вона утворює пористість. Для зварювання алюмінію вся пористість спричинена воднем (H2), таким же чином, як N2 працює у сталі.
Зварювальна пористість може проявлятися зовні або всередині (часто називається підповерхневою пористістю). Він також може розвинутися в одній точці зварного шва або по всій довжині, що призводить до слабких зварних швів.
Знання того, як визначити деякі ключові причини пористості та як швидко їх усунути, може допомогти покращити якість, продуктивність і кінцевий результат.
Погане покриття захисним газом
Погане покриття захисним газом є найпоширенішою причиною зварювальної пористості, оскільки це дозволяє атмосферним газам (N2 і H2) забруднювати зварювальну ванну. Відсутність належного покриття може виникнути з кількох причин, включаючи, але не обмежуючись цим, низьку швидкість потоку захисного газу, витоки в газовому каналі або занадто сильний потік повітря в камері зварювання. Надто висока швидкість також може бути причиною.
Якщо оператор підозрює, що причиною проблеми є низький потік, спробуйте відрегулювати витратомір газу, щоб переконатися, що швидкість адекватна. У разі використання режиму розпилення, наприклад, потоку від 35 до 50 кубічних футів на годину (cfh) має бути достатньо. Зварювання при більшій силі струму вимагає збільшення швидкості потоку, але важливо не встановлювати її надто високою. Це може призвести до турбулентності в деяких конструкціях гармат, що порушує покриття захисним газом.
Важливо зазначити, що гармати різної конструкції мають різні характеристики потоку газу (див. два приклади нижче). «Приємна точка» швидкості потоку газу для верхньої конструкції набагато більша, ніж для нижньої конструкції. Це те, що інженер зі зварювання повинен враховувати під час налаштування зварювальної камери.
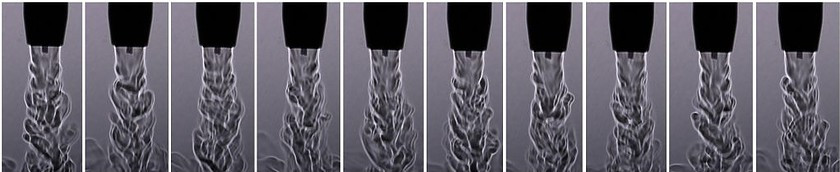
Схема 1 показує плавний потік газу на виході з сопла
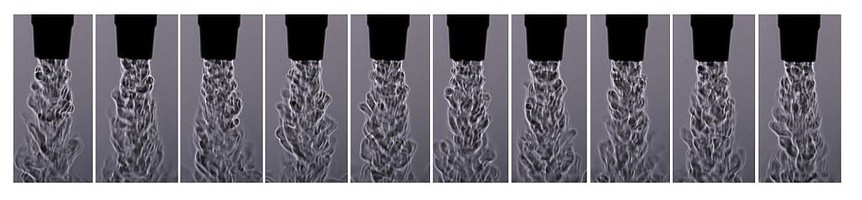
Схема 2 показує турбулентний потік газу на виході з сопла.
Також перевірте на наявність пошкоджень газовий шланг, фітинги та з’єднувачі, а також ущільнювальні кільця на штифті живлення зварювального пістолета MIG. За потреби замініть.
Використовуючи вентилятори для охолодження операторів або деталей у зварювальній камері, слідкуйте за тим, щоб вони не були спрямовані безпосередньо на зону зварювання, де вони можуть порушити покриття газом. Розмістіть екран у зварювальній камері для захисту від зовнішнього потоку повітря.
Ще раз торкніться програми в роботах, щоб переконатися, що відстань від наконечника до робочого місця є належною, яка зазвичай становить від ½ до 3/4 дюйма, залежно від бажаної довжини дуги.
Нарешті, знизити швидкість руху, якщо пористість не зникає, або проконсультуйтеся з постачальником MIG для різних передніх компонентів із кращим покриттям газу
Забруднення основними металами
Забруднення неблагородним металом є ще однією причиною появи пористості — від масла та мастила до окалини та іржі. Волога також може сприяти цьому розриву, особливо при зварюванні алюмінію. Ці типи забруднень зазвичай призводять до появи зовнішньої пористості, видимої оператору. Оцинкована сталь більш схильна до підповерхневої пористості.
Для боротьби із зовнішньою пористістю обов’язково ретельно очистіть основний матеріал перед зварюванням і розгляньте можливість використання зварювального дроту з металевим сердечником. Цей тип дроту має більший рівень розкислювачів, ніж суцільний дріт, тому він більш стійкий до будь-яких забруднень, що залишилися на основному матеріалі. Завжди зберігайте ці та будь-які інші дроти в сухому, чистому місці з такою ж або трохи вищою температурою, ніж рослина. Це допоможе звести до мінімуму конденсацію, яка може ввести вологу у зварювальну ванну та спричинити пористість. Не зберігайте дроти в холодних складах або на відкритому повітрі.
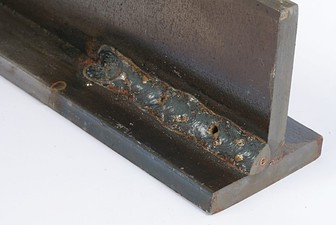
Пористість, розриви порожнистого типу, утворені захопленням газу під час затвердіння, є поширеним, але громіздким дефектом при зварюванні MIG, який має кілька причин.
Під час зварювання оцинкованої сталі цинк випаровується при нижчій температурі, ніж плавлення сталі, а висока швидкість руху призводить до швидкого замерзання зварювальної ванни. Це може затримувати пари цинку в сталі, що призведе до пористості. Боріться з цією ситуацією, контролюючи швидкість руху. Знову ж таки, розглянемо спеціально розроблений (формула флюсу) дріт із металевим сердечником, який сприяє виходу парів цинку зі зварювальної ванни.
Забиті та/або занижені сопла
Засмічені та/або занижені сопла також можуть спричинити пористість. Зварювальні бризки можуть накопичуватися в соплі та на поверхні контактного наконечника та дифузора, що призведе до обмеження потоку захисного газу або спричинить його турбулентність. Обидві ситуації залишають зварювальну ванну з неадекватним захистом.
Цю ситуацію ускладнює сопло, яке замале для застосування та більше схильне до більшого та швидшого розбризкування. Менші сопла можуть забезпечити кращий доступ до швів, але також перешкоджають потоку газу через меншу площу поперечного перерізу, дозволену для потоку газу. Завжди пам’ятайте про різну величину витиску (або заглиблення) контакту кінчика форсунки, оскільки це може бути ще одним фактором, який впливає на потік і пористість захисного газу при виборі сопла.
Пам’ятаючи про це, переконайтеся, що насадка достатньо велика для застосування. Як правило, застосування з високим зварювальним струмом із використанням дроту більших розмірів потребує насадки з більшим діаметром отвору.
У напівавтоматичному зварюванні періодично перевіряйте наявність зварювальних бризок у соплі та видаляйте їх за допомогою зварювальників (зварювальних машин) або замініть сопло, якщо необхідно. Під час цієї перевірки переконайтеся, що контактний наконечник у хорошому стані та що газовий дифузор має чисті газові отвори. Оператори також можуть використовувати суміш проти розбризкування, але вони повинні стежити, щоб не занурювати сопло в суміш занадто далеко або надовго, оскільки надмірна кількість суміші може забруднити захисний газ і пошкодити ізоляцію сопла.
Для роботизованої зварювальної операції інвестуйте в станцію очищення сопел або розгортку для боротьби з накопиченням бризок. Цей периферійний пристрій очищає сопло та дифузор під час звичайних пауз у виробництві, щоб не впливати на тривалість циклу. Станції очищення форсунок призначені для роботи в поєднанні з розпилювачем проти бризок, який наносить тонкий шар суміші на передні компоненти. Занадто багато або занадто мало рідини для захисту від бризок може призвести до додаткової пористості. Додавання повітряного обдуву до процесу очищення сопла також може допомогти у видаленні бризок із витратних матеріалів.
Збереження якості та продуктивності
Якщо стежити за процесом зварювання та знати причини пористості, впроваджувати рішення відносно просто. Це може допомогти забезпечити більший час увімкнення дуги, якісні результати та більше якісних деталей, що переміщуються у виробництво.
Час публікації: 02 лютого 2020 р